Duplex-Edelstahl 316L VS 2205 in der Biomedizin
Die pharmazeutische und biotechnologische Industrie stellt relativ hohe Anforderungen an die Stahlwerkstoffe, die in Verarbeitungsbehältern und Rohrleitungssystemen verwendet werden. Sie müssen eine ausgezeichnete Korrosionsbeständigkeit und Sauberkeit aufweisen, um die Reinheit und Qualität des Arzneimittels zu gewährleisten, und sie müssen auch in der Lage sein, die Produktionsumgebung und die Desinfektions- und Reinigungsprozesse bei Temperatur, Druck und Korrosion zu ertragen.
316L (UNS S31603, EN 1.4404) ist ein austenitischer rostfreier Stahl, der hauptsächlich für die Herstellung von Geräten in der pharmazeutischen und biotechnologischen Industrie verwendet wird. Edelstahl 316L verfügt über eine hervorragende Korrosionsbeständigkeit, Schweißbarkeit und elektrolytische Polierbarkeit, was ihn zu einem idealen Werkstoff für die meisten pharmazeutischen Anwendungen macht. Obwohl rostfreier Stahl 316L in vielen Prozessumgebungen gute Leistungen erbringt, verbessern die Kunden die Leistung von rostfreiem Stahl 316L weiterhin durch die sorgfältige Auswahl der spezifischen chemischen Zusammensetzung von rostfreiem Stahl 316L und den Einsatz verbesserter Produktionsverfahren wie dem Elektroschlacke-Umschmelzen (ESR).
Für stark korrosive Medien können Kunden, die höhere Wartungskosten in Kauf nehmen, weiterhin Edelstahl 316L verwenden oder sich für den Einsatz von 6%-Molybdän-Superaustenitstahl mit höherer Legierungszusammensetzung entscheiden, wie AL-6XN® (UNS N08367) oder 254 SMO® (UNS S31254, EN 1.4547). Gegenwärtig wird auch der zweiphasige rostfreie Stahl 2205 (UNS S32205, EN 1.4462) für die Herstellung von Prozessanlagen in dieser Industrie verwendet.
Das Gefüge des rostfreien Stahls 316L umfasst die Austenitphase und eine sehr geringe Menge an Ferritphase, die hauptsächlich durch die Zugabe einer ausreichenden Menge an Nickel zur Stabilisierung der Austenitphase gebildet wird. Der Nickelgehalt von rostfreiem Stahl 316L beträgt im Allgemeinen 10-11%. Der rostfreie Duplexstahl 2205 entsteht durch die Verringerung des Nickelgehalts auf etwa 5% und die Anpassung des Mangans und des Stickstoffs, um etwa 40-50% Ferrit zu bilden, und enthält ungefähr die gleiche Menge an Ferrit- und Austenitphasengefüge, mit großer bis erheblicher Korrosionsbeständigkeit. Der höhere Stickstoffgehalt und das feinkörnige Gefüge des nichtrostenden Duplexstahls 2205 bewirken, dass er eine höhere Festigkeit aufweist als die üblichen austenitischen nichtrostenden Stähle wie 304L und 316L. Unter Glühbedingungen ist die Streckgrenze von nichtrostendem Duplexstahl 2205 etwa doppelt so hoch wie die von nichtrostendem Stahl 316L. Aufgrund dieser höheren Festigkeit kann die zulässige Spannung von rostfreiem 2205-Duplex-Stahl je nach den Konstruktionsspezifikationen für die Fertigungsanlagen viel höher sein. Bei vielen Anwendungen kann er die Wandstärke und die Kosten reduzieren. Sehen wir uns die chemische Zusammensetzung und den Vergleich der mechanischen Eigenschaften von 316L und 2205 an (gemäß ASTM A240)
Klassen | UNS | C | Mn | P | S | Si | Cr | Ni | Mo | N |
316L | S31603 | 0.03 | 2.0 | 0.045 | 0.03 | 0.75 | 16.0-18.0 | 10.0-14.0 | 2.0-3.0 | 0.1 |
2205 | S32205 | 0.03 | 2.0 | 0.03 | 0.02 | 1.0 | 22.0-23.0 | 4.5-6.5 | 3.0-3.5 | 0.14-0.2 |
Klassen | Zugfestigkeit, Mpa(ksi) | Streckgrenze Mpa(ksi) | Dehnung | Härte, HRB(HRC) |
316/316L | 515(75) | 205(30) | 40% | 217(95) |
2205 | 655(95) | 450(65) | 25% | 29331() |
Leistung der Korrosivität
Beständigkeit gegen Lochfraß
In pharmazeutischen und biotechnologischen Anwendungen ist die häufigste Korrosionsart von Edelstahl Lochfraß in chloridhaltigen Medien. Der nichtrostende Duplexstahl 2205 weist einen höheren Chrom-, Molybdän- und Stickstoffgehalt auf und ist in Bezug auf die Beständigkeit gegen Lochfraß und Spaltkorrosion deutlich besser als der nichtrostende Stahl 316L. Die relative Korrosionsbeständigkeit von nichtrostendem Stahl kann durch Messung der Temperatur (kritische Korrosionstemperatur) bestimmt werden, die für Lochfraß in einer Standard-Testlösung aus 6% Eisenchlorid erforderlich ist. Die kritische Korrosionstemperatur (CPT) des nichtrostenden Duplexstahls 2205 liegt zwischen dem nichtrostenden Stahl 316L und dem superaustenitischen Molybdänstahl 6%. Es ist zu beachten, dass die in Eisenchloridlösung gemessenen CPT-Daten eine zuverlässige Einstufung der Beständigkeit gegen Lochfraß durch Chloridionen darstellen und nicht zur Vorhersage der kritischen Korrosionstemperatur des Werkstoffs in anderen Chloridumgebungen verwendet werden sollten.
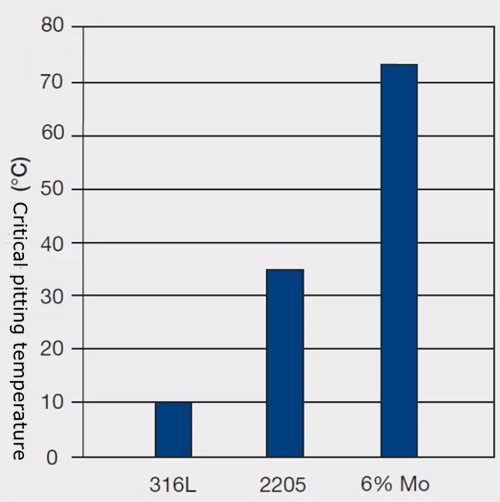
Spannungsrisskorrosion
Bei Temperaturen über 60°C (150°F) neigt Edelstahl 316L unter der kombinierten Wirkung von Zugspannung und Chloridionen zur Rissbildung, und diese katastrophale Korrosion wird als Chlorid-Spannungsrisskorrosion (SCC) bezeichnet. Bei der Auswahl von Werkstoffen für heiße Flüssigkeiten sollte nichtrostender Stahl 316 in Gegenwart von Chloridionen und bei Temperaturen von 60°C oder mehr vermieden werden. Wie in der nachstehenden Abbildung dargestellt, kann nichtrostender Duplexstahl 2205 in einer einfachen Salzlösung bei mindestens 120°C (250°F) SCC widerstehen.
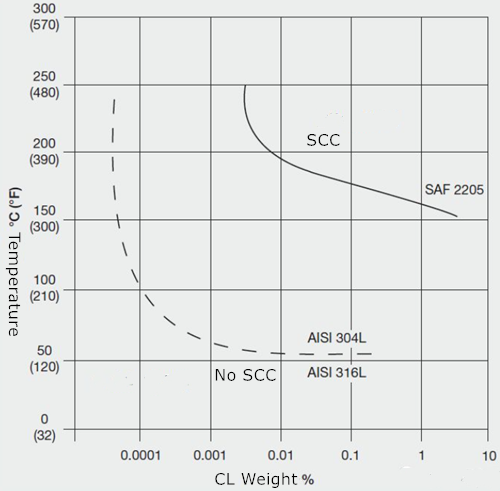
Verarbeitungseigenschaften
Die Bearbeitung von nichtrostendem Duplexstahl 2205 ähnelt in vielerlei Hinsicht der von 316L, aber es gibt dennoch einige Unterschiede. Bei der Kaltumformung müssen die höhere Festigkeit und die Kaltverfestigung des nichtrostenden Dualphasenstahls berücksichtigt werden, die Ausrüstung muss unter Umständen eine höhere Belastbarkeit aufweisen, und im Betrieb zeigt nichtrostender Stahl 2205 eine höhere Elastizität als austenitische Standard-Edelstahlsorten. Die höhere Festigkeit des nichtrostenden Duplexstahls 2205 erschwert das Schneiden im Vergleich zu 316L.
Der nichtrostende Duplexstahl 2205 kann auf die gleiche Weise geschweißt werden wie der nichtrostende Stahl 316L. Allerdings müssen die Wärmezufuhr und die interlaminare Temperatur streng kontrolliert werden, um das erwartete Austenit-Ferrit-Phasenverhältnis aufrechtzuerhalten und die Ausscheidung von schädlichen intermetallischen Phasen zu vermeiden. Um diese Probleme zu vermeiden, enthält das Schweißgas einen geringen Anteil an Stickstoff. Bei der Schweißqualifizierung von nichtrostendem Duplexstahl wird üblicherweise das Austenit-Ferrit-Verhältnis mit Hilfe eines Ferritprüfgeräts oder einer metallografischen Untersuchung ermittelt. Die Prüfmethode ASTM A 923 wird üblicherweise verwendet, um das Vorhandensein schädlicher intermetallischer Phasen zu überprüfen. Der empfohlene Schweißzusatzwerkstoff für die Schweißung ist ER2209 (UNSS39209, EN 1600). Selbstschmelzschweißen wird nur empfohlen, wenn die Schweißlösung nach dem Schweißen geglüht werden kann, um die Korrosionsbeständigkeit wiederherzustellen. Es wird kein Zusatzwerkstoff verwendet. Für das Lösungsglühen werden die Bauteile auf eine Temperatur von mindestens 1040°C (1900°F) erhitzt und dann schnell abgekühlt.
Die Eindringtiefe und das Fließverhalten von rostfreiem Duplexstahl 2205 sind schlechter als bei rostfreiem Stahl 316L, so dass die Schweißgeschwindigkeit langsamer ist und die Form der Verbindung angepasst werden muss. Der nichtrostende Duplexstahl 2205 erfordert einen breiteren Fugenwinkel, einen größeren Wurzelabstand und eine kleinere stumpfe Kante als der nichtrostende Stahl 316L, um eine vollständig geschmolzene Schweißnaht zu erhalten. Wenn die Schweißanlage die Verwendung von Schweißdraht zulässt, muss die 2209 Fülldraht wird für das Schweißen von Rohren aus rostfreiem Stahl 2205 verwendet, oder der Schweißdraht kann anstelle des entsprechenden Legierungszusatzes verwendet werden.
Elektrolytisches Polieren
Bei vielen pharmazeutischen und biotechnologischen Anwendungen muss die Oberfläche, die mit dem Produkt in Berührung kommt, elektrolytisch poliert sein, so dass hochwertige elektrolytisch polierte Oberflächen eine wichtige Materialeigenschaft sind. 2205 Duplex-Edelstahl kann elektrolytisch auf eine Oberfläche von 15 Mikrozoll (0,38 Mikrometer) oder mehr poliert werden, was die ASME BPE-Norm für die Oberflächengüte elektrolytisch polierter Oberflächen übertrifft. Die elektrolytisch polierte Oberfläche von 2205-Edelstahl ist jedoch nicht so glänzend wie die von 316L-Edelstahl. Dieser Unterschied ist auf die etwas höhere Metalllöslichkeit von Ferrit im Vergleich zu Austenit während des Elektropolierens zurückzuführen.